A Brief History of Plastic & Material Types
Since there is no universally accepted definition of plastic, it is difficult to determine an exact date for the invention of plastic. In fact, you can find references throughout antiquity and even in the Old Testament of natural substances being manipulated for use as adhesives and various coatings. However, it can generally be said that the precursor to the modern plastics industry began in the mid 1800’s with the discovery and development of hard rubber and other cellulose compounds. The first use of plastic in the form of a synthetic polymer that most of us would recognize as plastic today, would be the development of Bakelite in the early 1900’s.
In an era where the use of plastics is routinely demonized for its environmental impacts, it is interesting to point out, that one of the chief driving forces for the development of modern plastics was an effort to protect wildlife, or more specifically, African elephants. By the mid 1800’s, African elephants were being slaughtered at an alarming and unsustainable rate of 70,000 animals per year for their ivory. In 1865, a billiard ball manufacturer offered a reward for the development of a product that would replace ivory in the manufacture of billiard balls. John Wesley Hyatt, a 28 year old American entrepreneur, developed an answer to this challenge by using a compound called nitrocellulose in a process to manufacture the first commercially viable synthetic billiard balls.
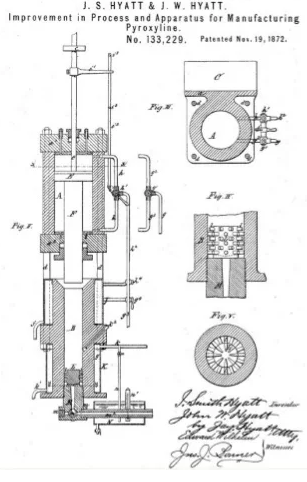
Modern plastics can be broken down into two main groups; thermosets and thermoplastics. Thermosets began with the Bakelite type polymers of the early 1900’s. A key characteristic of thermosets is that they can be melted and molded only once. Once they have solidified, an irreversible cross-linking occurs at the molecular level. Alternately, Thermoplastics do not generally undergo chemical changes when they are melted and molded and can therefore be melted and reformed again and again. This is a key characteristic when it comes to the recyclability of a specific type of plastic.
The vast majority of plastics used in industry today fall into the thermoplastic group of materials. From here, thermoplastics can be generally separated into two categories; amorphous resins and crystalline resins.
Amorphous Resins
Amorphous resins have a minimally crystalline structure by nature with a randomly arranged molecular structure. The molecular structure of amorphous resins in relation to the wavelength of visible light typically makes them transparent to translucent in their natural state. They exhibit great dimensional stability in molding with very low warpage due to isotropic shrinkage. Poor chemical resistance is an inherent weakness of many amorphous resins. Some examples of amorphous resins are:
- Polyethersulfone (PES)
- Polyetherimide (PEI)
- Polysulfone (PSU)
- Polycarbonate (PC)
- PC/ABS
- Acrylonitrile Butadiene Styrene (ABS)
- Styrene Acrylonitrile (SAN)
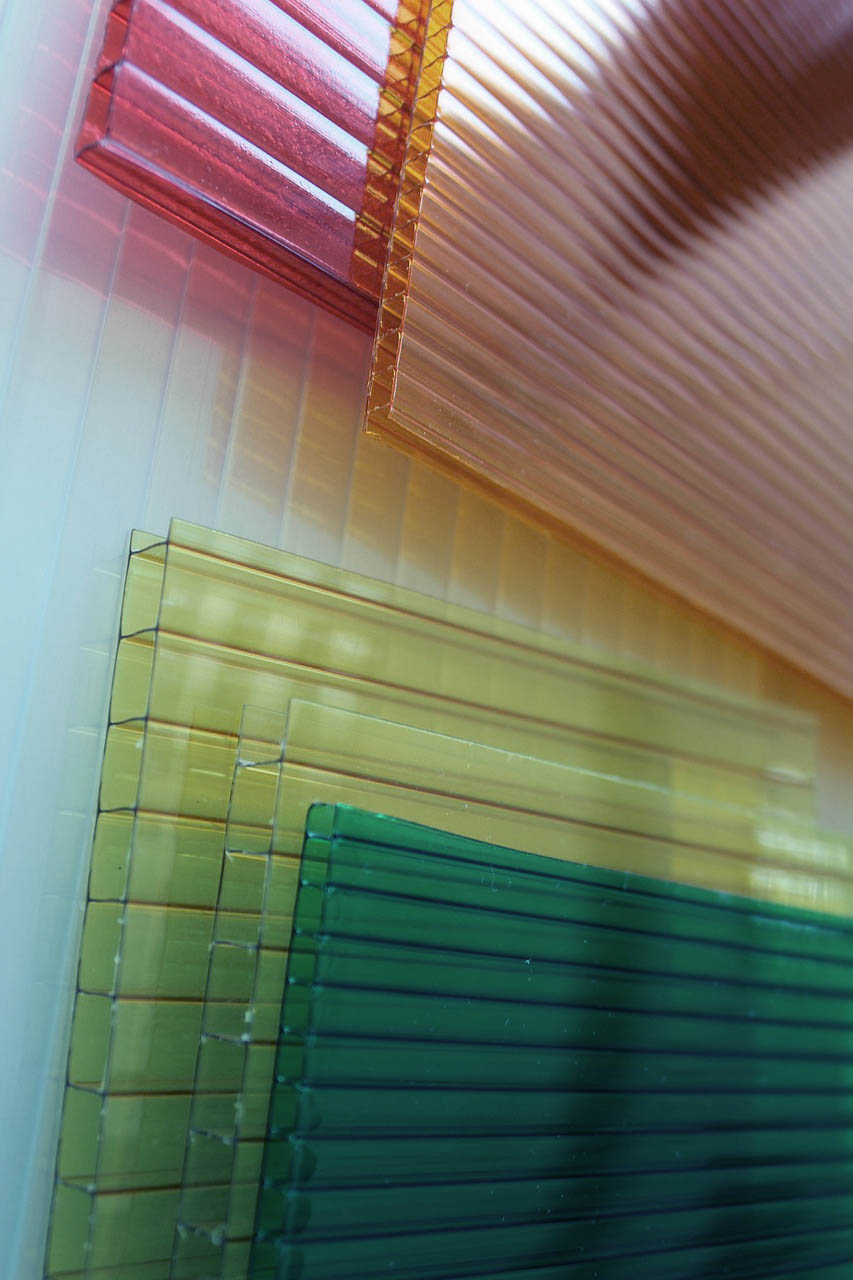
Crystalline Resins
Crystalline resins have an extensively crystalline structure by nature with their molecular structure exhibiting a more ordered pattern. The structure size relative to the wavelength of visible light typically makes crystalline resins translucent to opaque in their natural state. They have a lower dimensional stability in molding (higher warpage due to anisotropic shrinkage) compared to amorphous resins. Crystalline resins generally have excellent chemical resistance properties (especially high temp resins). Some examples of crystalline resins are:
- Polyetheretherketone (PEEK)
- Perfluoroalkoxy (PFA)
- Polyphenylene Sulfide (PPS)
- Ethylenetetrafluoroethylene (ETFE)
- Polyphthalamide (PPA)
- Polybutyleneterephthalate (PBT)
- Nylon (PA)
- Acetal
- Polypropylene (PP)
- Polyethylene (PE)
- Thermoplastic Urethane (TPU)
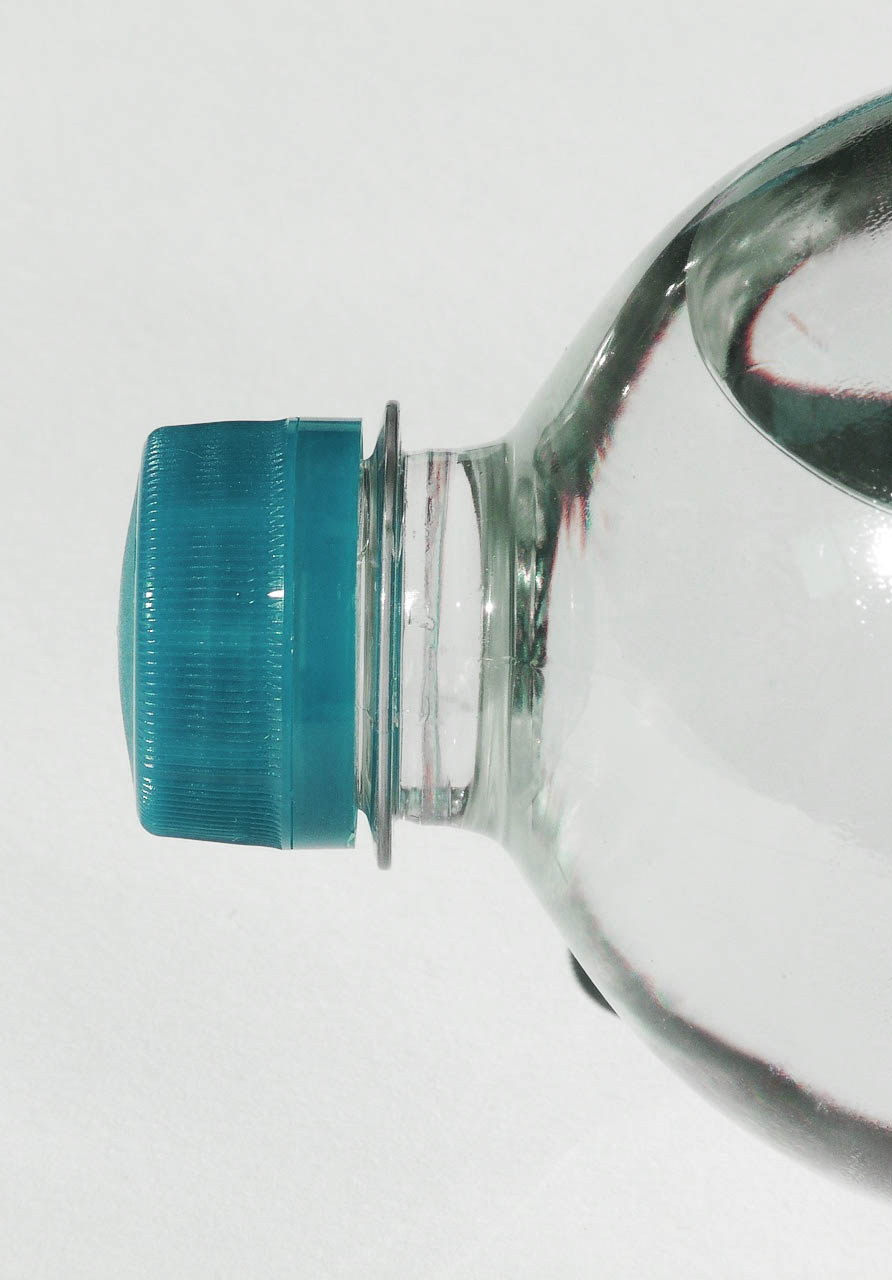
Both amorphous and crystalline resins can take on additional, different, and improved properties with the addition of reinforcements and fillers. The addition of carbon fibers or glass fibers to resins can provide increased strength and durability. For example, with the addition of additives, the tensile strength of amorphous resins can increase up to 250 percent and the flexural modulus can increase up to 400 percent. After molding, filled amorphous resins will typically shrink 0.001”- 0.003” compared to 0.005”- 0.007” when unfilled. In crystalline resins, with the addition of additives, the tensile strength of the resin can increase up to 400 percent and the flexural modulus can increase up to 700 percent. After molding, filled crystalline resins will typically shrink 0.002”- 0.007” compared to 0.012”- 0.023” when unfilled.
Examples of available fillers for plastic resins include:
- PTFE
- Silicone
- MoS2Aramid
- Stainless steel
- Chopped carbon fiber
- Milled carbon fiber
- Polymeric alloys
- Minerals
- Glass beads
- Milled glass fibers
In addition to improved strength, these fillers can also impart specific characteristics in a base resin such as improved lubricity, conductivity, and dimensional stability. As with all additives, there are pros and cons with their usage. Glass fibers, one of the most common fillers, can provide a resin with increased dimensional stability, stiffness and strength. However, the more the glass loading of a resin is increased, the more prone it becomes to catastrophic failure when exposed to extreme stresses.
Another example would be the addition of carbon fiber. Carbon fiber provides the highest strength to weight ratio of any reinforcement filler currently available. It can also impart properties such as electrical conductivity, EMI/RFI shielding, and improved thermal conductivity, and wear performance. Carbon fibers however, can be a fairly expensive additive and can promote shrink differential causing part warpage.
In the world of modern plastics, there is an almost endless array of options and combinations that can be formulated to suit the needs of science, industry, and our daily lives. If you have specific material requirements for a particular product, we’d be happy to discuss your needs further and assist you in making the right material selection.